Optimization phase
To improve the overall performance of the product, from the point of view of lightness and raw material cost, we ran Altair Inspire, a structural optimization software. Giving as input a raw geometry of the component we're interested in, and applying forces and constraint, the software computed the best possible shape. That is to say: a shape with the minimum possible volume, able to resist to the imposed stresses.
The optimization of the whole frame led to a lost in weight of about 4 kilograms, that is almost the 20% of the total. The loss in weight is a crucial point for us, since a lighter sitski is more responsive and easier to transport.
FEM Analysis
Throughout the optimization process we performed several FEM analysis on the different parts. We used Autodesk Simulation 360, a cloud-based software that gave us the possibility to run also "heavy" computations, i.e. meshes with an high number of elements, since the calculation process is left to Autodesk's servers and not to our personal computers.
We considered different stress cases for every component, always considering a rider's mass of 130 kilograms. We evaluated the overall external forces through a "dynamic equilibrium" approach (equilibrium of centrifugal force and gravitational force during a turn), and a raw approximation of the inertial forces generated when passing over a bump in the slope (for which we found a mathematical expression). The stresses always remained way under the 500 MPa limit, given by the Yeld Strenght of Aluminum 7075.
However a more precise analysis should be based on an accurate dynamic analysis of the system, which we included in the further improvements section.
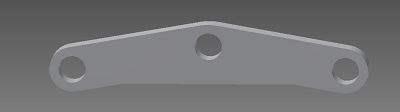
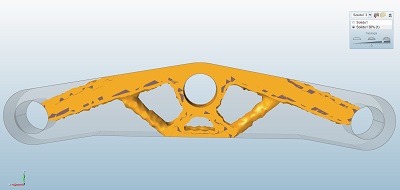
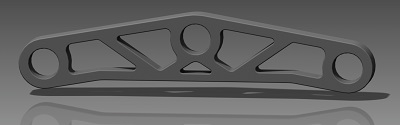
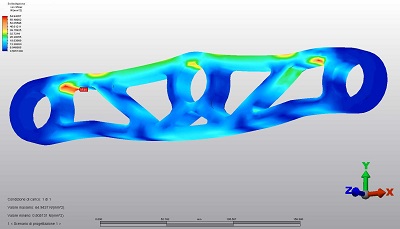