Il
sistema di controllo ha lo scopo di realizzare una portata di abrasivo
costante durante la lavorazione, mantenendo il valore impostato,
in modo da poter realizzare lavorazioni con un grado di finitura
superficiale pressoché uniforme. Infatti la finitura superficiale
delle parti lavorate dipende dalla portata di abrasivo iniettata
nella camera di miscelazione.
Come noto,
nei sistemi di adduzione dell'abrasivo a gravità, la portata
di abrasivo in uscita dalla tramoggia è fortemente influenzata
dalla quantità di abrasivo presente nella tramoggia stessa;
in particolare al diminuire del livello di abrasivo diminuisce
anche la portata d'uscita, ovviamente a pari sezione di passaggio.
Si può
quindi pensare di adottare un sistema di controllo in modo da
variare l'area di passaggio dell'abrasivo in funzione della quantità
di abrasivo presente nella tramoggia, in modo da ottenere una
portata di erogazione costante o comunque variabile entro un ristretto
intervallo.
Per misurare
la quantità di abrasivo presente nella tramoggia ed in
particolare la variazione di tale quantità nell'unità
di tempo (portata di abrasivo erogata), si è pensato di
misurare la variazione di massa del sistema tramoggia + abrasivo.
In funzione di tale variazione si agirà sul sistema di
controllo dell'apertura della feritoia, attraverso la quale fuoriesce
l'abrasivo.
Un sistema
di controllo così fatto è realizzabile mediante
l'uso di un sistema di misura della massa (cella di carico) agente
sulla tramoggia contenente l'abrasivo.
Tale sistema inoltre permette di realizzare una retroazione continua
del segnale di controllo della portata. Infatti misurando continuamente
la variazione della massa della tramoggia è possibile conoscere
in ogni momento la portata di abrasivo che è stata erogata
e di conseguenza, se essa si discosta dal valore desiderato, operare
una correzione continua per mantenere la portata di abrasivo entro
un intervallo di valori adeguato.
I problemi
principali che sino ad ora hanno impedito la realizzazione di
una retroazione completa risiedono nel fatto che spesso si è
cercato di valutare la portata del getto idroabrasivo all'uscita
dal focalizzatore, incontrando non poche difficoltà:
·
la velocità del getto di sola acqua è circa tre
volte quella del suono in aria; nel getto idroabrasivo, sebbene
la velocità risulti molto minore (circa 1/3), rimane comunque
molto elevata e quindi misurabile solo per mezzo di apparecchiature
complesse e molto costose.
· studi condotti in passato hanno dimostrato che la distribuzione
delle velocità delle particelle nel getto è assimilabile
ad una distribuzione normale attorno all'asse del getto stesso,
ma le misure effettive di questa distribuzione non sono calcolabili
con certezza.
Un altro
ostacolo alla realizzazione di sistemi controllo della portata
di abrasivo è stato l'aspetto tecnico-economico. Le soluzioni
fino ad ora individuare erano difficilmente realizzabili in pratica
a causa della loro complessità e/o del loro non trascurabile
costo economico (soprattutto se rapportato al costo dell'intero
sistema AWJ).
In questa
ottica la soluzione proposta risulta essere economica, grazie
alla semplicità dei componenti aggiuntivi richiesti, semplice
da realizzare e facilmente gestibile dall'unità di governo
della macchina.
La cella
di carico fornisce in uscita un segnale elettrico proporzionale
alla massa misurata, questo segnale viene trasferito ad una unità
di controllo (per esempio un calcolatore, ma nell'ottica di integrazione
del sistema con la macchina sarà l'unità di governo
della macchina stessa) che lo elabora e determina la portata di
abrasivo che è stata erogata. Il sistema di governo a sua
volta genera un segnale di comando che viene inviato al dispositivo
di erogazione dell'abrasivo (che può essere un servomotore
che comanda una vite micrometrica).
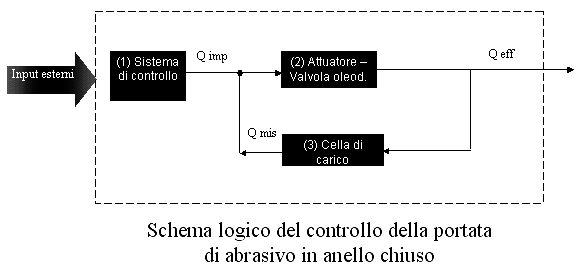
In
sintesi i vantaggi del sistema di controllo della portata di abrasivo
proposto sono i seguenti:
¨ maggiore
livello qualitativo della lavorazione, in termini di uniformità
delle superfici (rugosità superficiale, conicità
del solco di taglio, profondità di lavorazione;
¨ semplicità
di realizzazione e messa a punto;
¨ possibilità
di variare il valore desiderato di portata dell'abrasivo anche
durante la lavorazione;
¨ possibilità
di essere applicato anche agli impianti AWJ esistenti;
¨ flessibilità:
intesa come capacità del sistema di adattarsi a tutte le
condizioni ambientali possibili (temperatura, umidità,
etc.), ed intesa come capacità di controllare la portata
per qualsiasi mesh di abrasivo;
¨ rispetto
agli altri sistemi proposti presenta il vantaggio di poter effettuare
una continua taratura dinamica delle condizioni di erogazione,
diminuendo i tempi di power off della macchina ed aumentando quindi
la produttività;
¨ il
sistema è in grado di tenere in considerazione anche disturbi
e variabili che non sono collegati al processo, per esempio la
quantità di abrasivo presente nella tramoggia che influenza
in maniera considerevole la portata di erogazione;
¨ massimo
livello di integrazione con l'unità di governo: il sistema
può essere controllato dal CNC (Controllo Numerico Computerizzato)
che gestisce la macchina, in modo da garantire la gestione dell'erogazione
dell'abrasivo in ogni lavorazione;
¨ il
controllo può essere applicato alla tramoggia principale
oppure ad una sotto tramoggia;
¨ il
riempimento della tramoggia con l'abrasivo può essere effettuato
anche senza arrestare la macchina, è sufficiente portare
la testa di taglio fuori dalla zona occupata dal pezzo in lavorazione
e molto rapidamente si può rabboccare l'abrasivo; tale
operazione risulta inoltre facilmente automatizzabile;
¨ costi
contenuti: a livello di produzione industriale del sistema gli
oneri aggiuntivi rispetto alla situazione attuale sono legati
alla presenza della cella di carico (che è un componente
molto diffuso ed economico) ed alla necessità di aggiornare
il software di gestione della macchina (intervento da effettuare
una tantum).